For a great many years I have been playing around with the idea of building a teardrop camping trailer. My design for a teardrop has evolved over the years and has been sitting either in model form on my desk or in illustrations that I've created using Blender 3D. I would work on the design from time to time and then let it sit idle as a lot of projects do that have to wait for either the right time, place or money to even start such a huge project.
I woke up the other morning and had a flash of inspiration concerning this long planned project that I pulled out of mothballs once again and have been working on it. To show you what I have in mind I will have to let you see some of my earlier work and plans for this project to get you up to speed as to where I am at today.
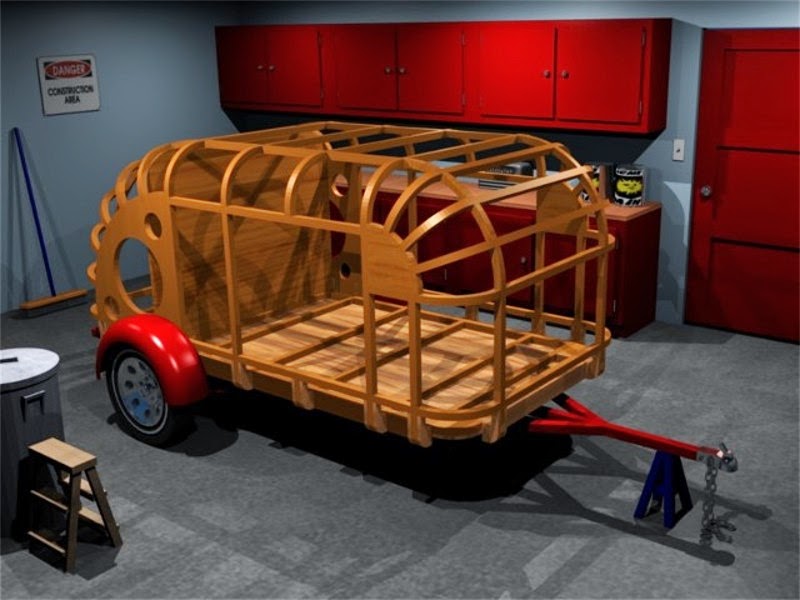
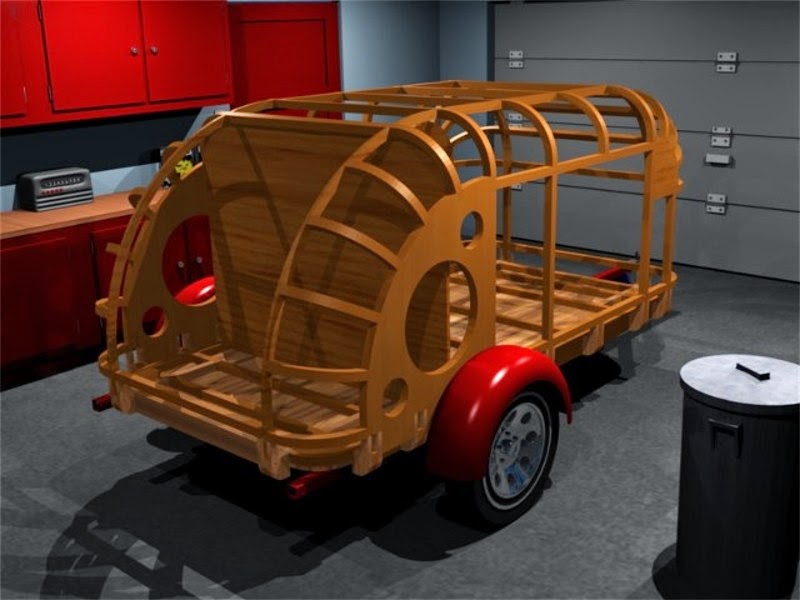
Here are two early computer models of the trailer that I have planned. These models were created in Blender 3D software which I am a big fan and as you can see does a great job of rendering something that looks close to a photograph. This early version of the trailer used all wood construction. The trailer that I have planned is larger than a conventional teardrop as it sits on a 5' X 10' trailer chassis to allow much more room in the forward sleeping cabin. My design is a cross between an all aluminum"Airstream" trailer and a teardrop. A normal teardrop has flat sides and no radius on the edges as shown here. This design I think gives it a much more pleasing smooth shape. The problem with it being constructed in wood as you see here is getting all the radius parts made and assembled. That just for starters kind of makes this type of build a real problem. Not that it could not be done just would be a lot of work and then you'd still have to figure out how to skin the body.
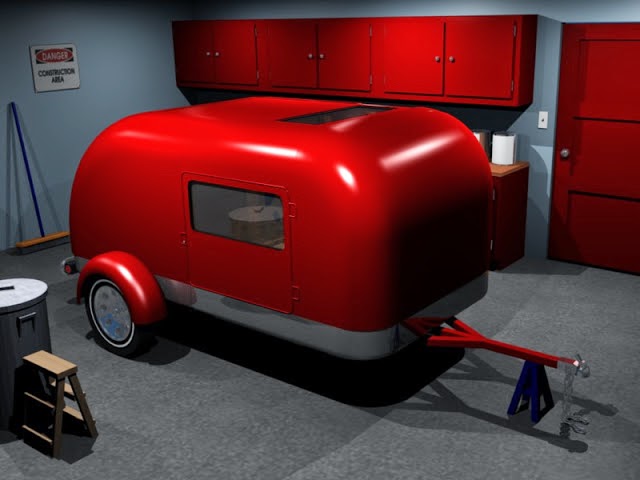
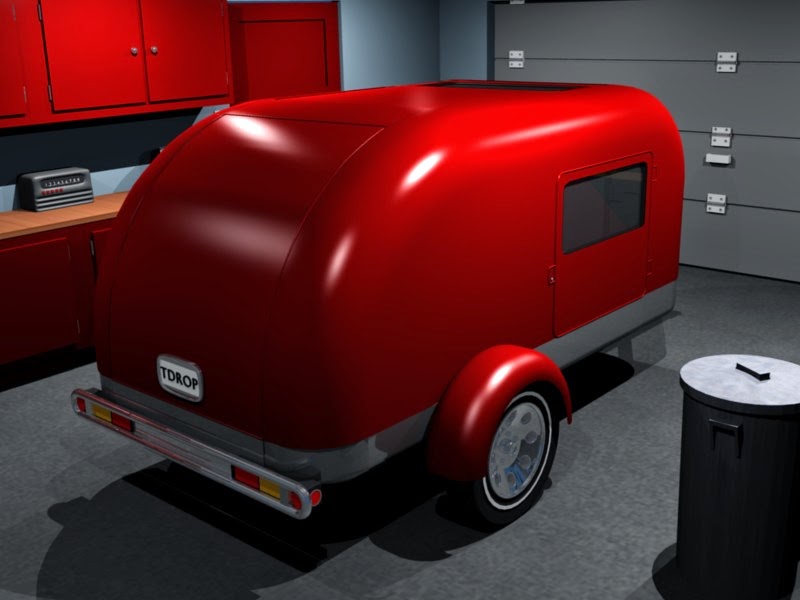
These next two images give you a much better idea of how the teardrop trailer would look once a skin was assembled on to the inner framework. A very slick looking trailer to say the least. This earlier version is very close to the idea that I have had in my head for the last 15 or 20 years. So it was a good start. At the time these computer models were created I did not know how to work with fiberglass composite construction. This changed after some training and several projects that have followed such as my motorcycle cargo trailer, a three section kayak, and the velomobile project. (See earlier post about the construction of these fiberglass composite projects.)
With all that I have learned from these projects and other smaller ones it finally hit me that the teardrop trailer could be built the same way. So the project idea is still alive and I am still planning on it's construction some time in the future. I have the space, and the time. Now just to work out the budget and I will have the three key steps in place to finally build what I call "The Teardrop Trailer Holy Grail Project."
The project would start off with a 5' X 10' steel frame. This I can buy already built. Why reinvent the wheel if you can get it already made? Makes things a lot simpler if this is sitting in the garage ready to be built upon and I don't have to worry about it being strong enough or that it may possibly track down the road incorrectly.
Next comes the fiberglass composite floor and fender assembly. This is exactly how the body for my motorcycle cargo trailer was built only much larger. The small squares in the floor of the trailer image you see above are the mounting points for the body to be attached to the frame. These mounting points are a hard mount that are glassed into the fiberglass/foam composite bed. This mount makes a solid strong mount to bolt the floor of the body to the frame once everything has been lined up for installation.
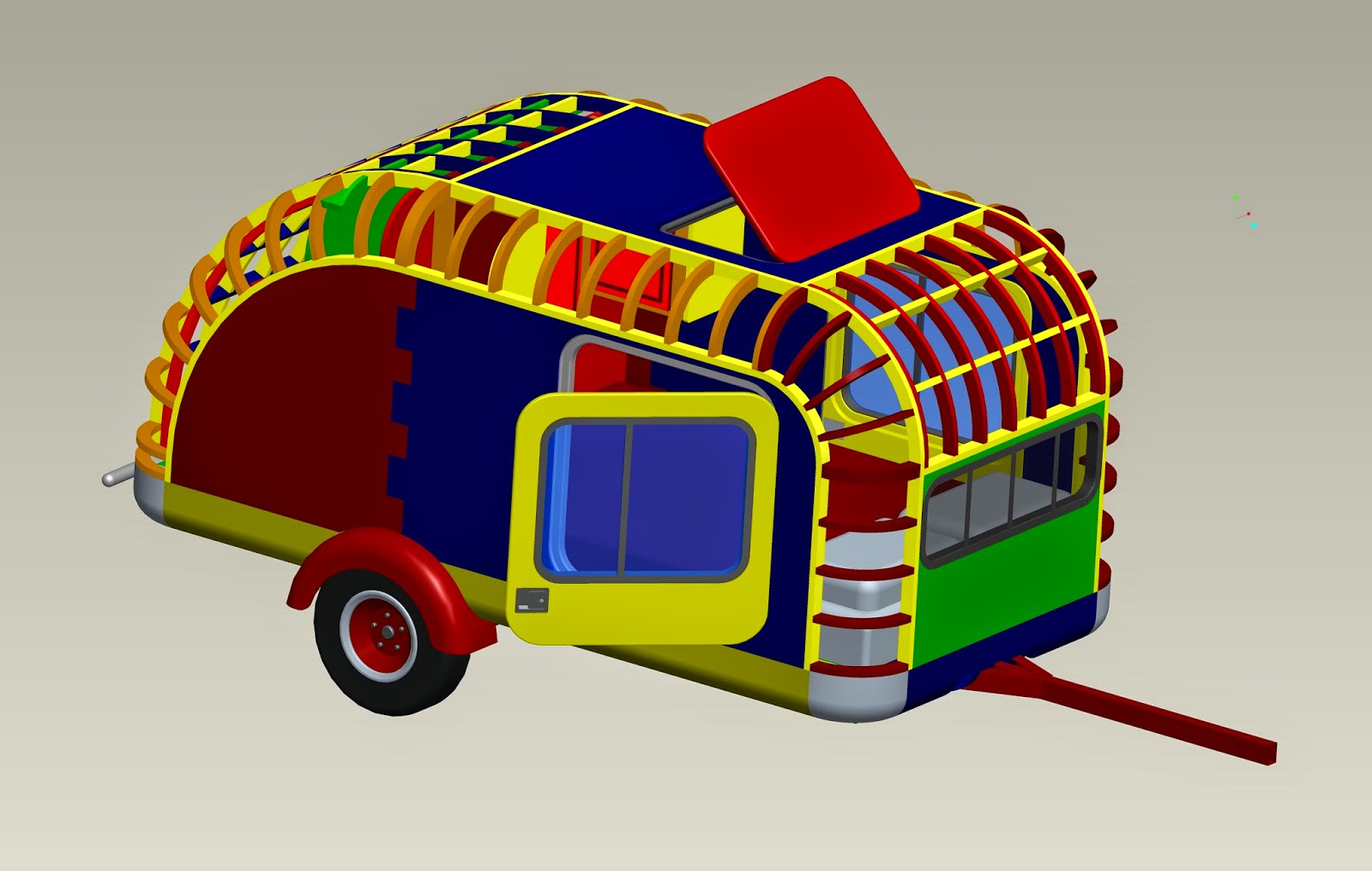
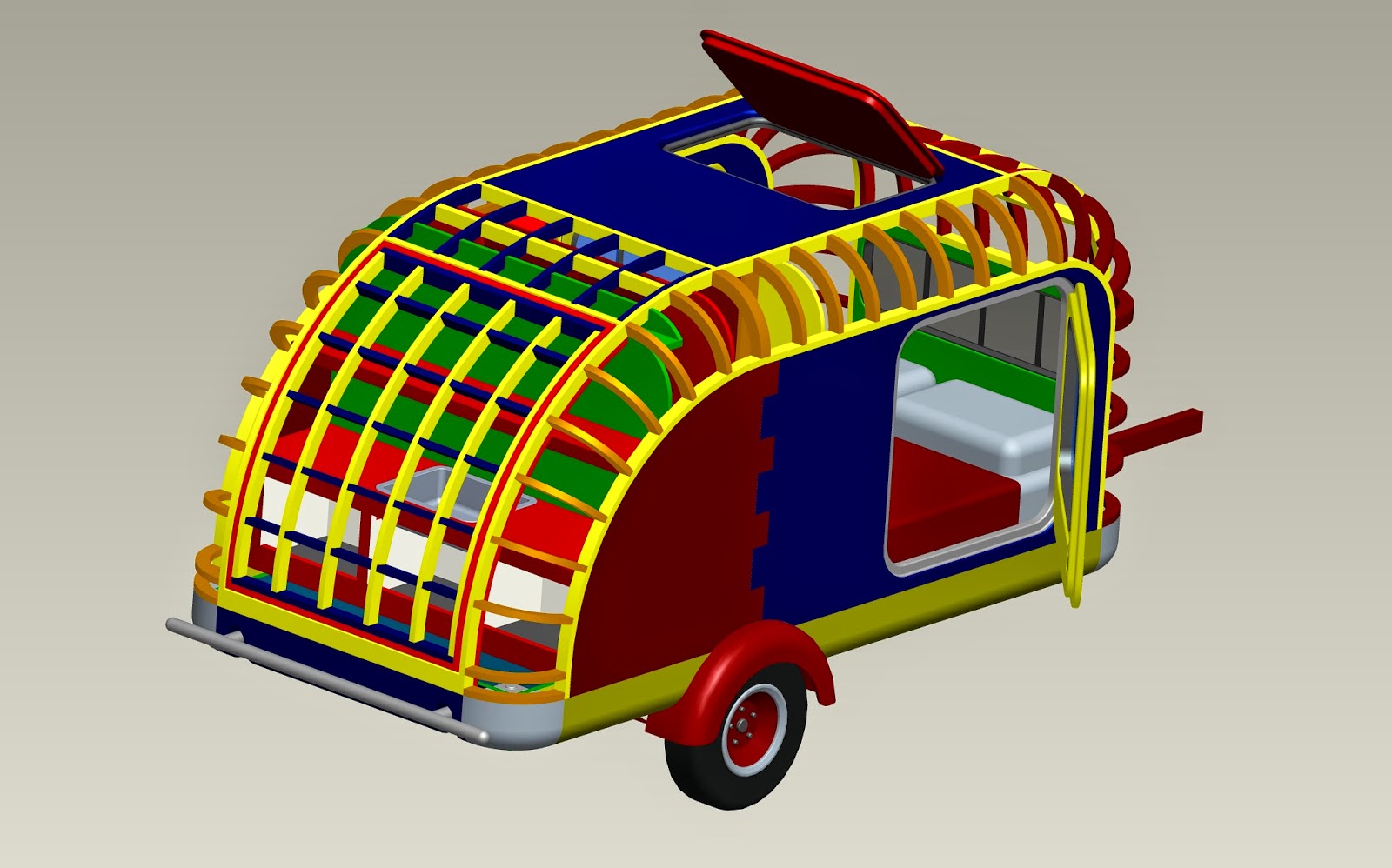
Next the body is fiberglassed on to the floor of the trailer. The curved pieces that make up the radius edges of the trailer along with all the other multi-colored parts you see in the above image are made from styrofoam that has been covered with fiberglass. Very light weight and strong once assembled. The curved pieces are small enough to be cut using my CNC machine so to make 46 of the needed parts would be easy work and all of them would be exactly the same shape and size for the project.
In this image you can see that the rear hatch has been removed and the kitchen cabinets and sink have been installed. Also in the image the bed has been installed into the forward sleeping area.
These two images give you a better idea of the overall shape of the body of the teardrop camping trailer. Once all of the framework of the trailer has been constructed the body is skinned with 1/4" thick strips of styrofoam much like a cedar strip canoe would be built and the same process that I used to make the body for my velomobile project. The body is then fiberglassed on the inside of the trailer, then sanded smooth on the outside and glassed once again. This makes a very lightweight and strong body that can then be sanded smooth and painted just as you would any vehicle.
An interior for the trailer is still in the planning stages as is much of this project. But with the answer to the problem of building the radius edges on the body it has come just that much closer to becoming a reality some day.
Another feature that I thought would be a big plus in the planning of this project is to have a built in water tank for the kitchen in the rear of the trailer. This would hold approximately 20 gallons of fresh water for cooking and cleaning. Along with the kitchen and the rest of the trailer for that matter would be a full electrical system for lighting and appliances. With the trailer being as large as it is there is even room for a closet to store clothing and items in the sleeping compartment. A nice feature to be sure.
The trailer would stand 6'4" tall and be 73" wide at the fenders. Overall length from the hitch to the rear bumper would be just a shade over 15' long. The sleeping compartment would be 5'2" x 9.5' in size with a ceiling height of 50" without the mattress. With these measurements it gives the sleeping compartment much more room than a standard teardrop trailer would have.
Lots of planning still needs to be done to even start this project. Right now my guess is that this project would take close to two years to complete at a cost of near $5000. I have the time and the space as I've said. I just have to come up with the funding for this along with a vehicle that can tow it. It would be very light weight in the scheme of things but is still way to large to tow with my Mini Cooper. My Mini has the power but it still would be scary as you could not see around this trailer when you towed it. Not a good idea for sure.
I will continue refining the project from time to time and when I do finally set the starting date as to it's construction I will be sure to let you know. In the meantime I thought I'd wet you appetite with this little beauty. If you have any suggestions or ideas that I should include in this project I would be more than happy to hear from you. Have a good one!